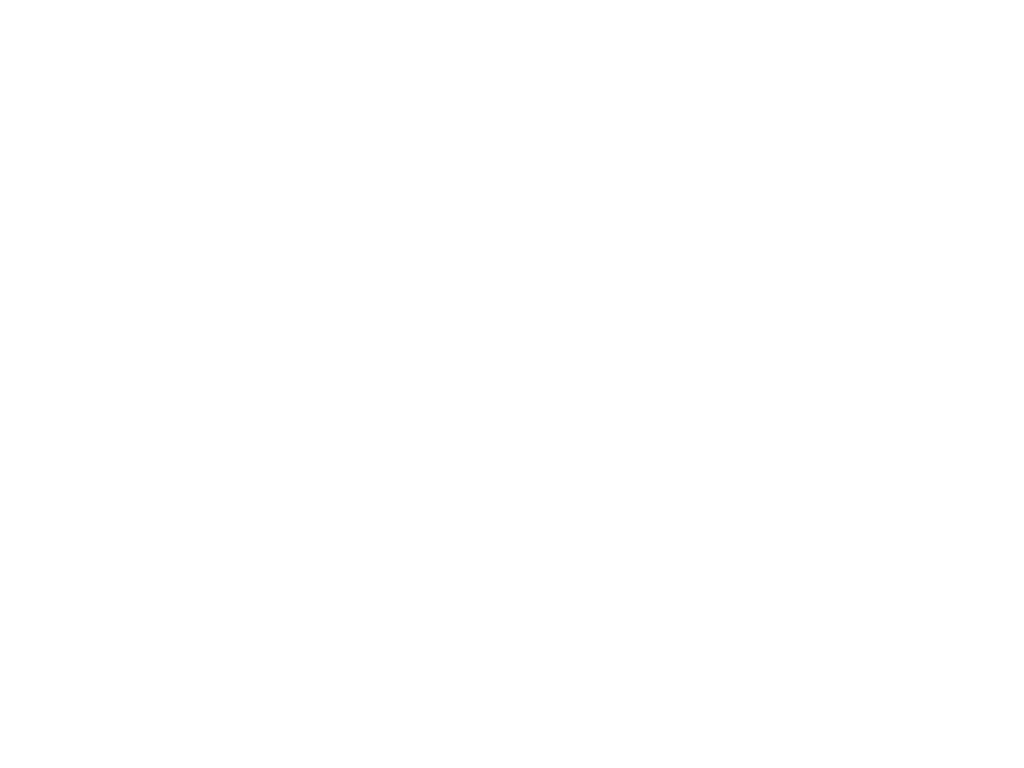
HOLISTIC
We are all about sustainability We have made significant progress in our mission to produce climate-neutral implants and have already adopted a wide range of measures to this end. We generate our own power to which we have connected our production sites for heat management.
ENVIRONMENT FRIENDLY
Königsee Implantate generates its own renewable solar energy with photovoltaic technology at each of its 5 sites. This has a positive impact on our carbon footprint. We use the energy we generate for our internal production. Any excess at peak times is fed back into the grid.
SUSTAINABLE
We focus on sustainable packaging made of up to 100% recycled paper. This means we completely avoid the use of virgin fibres. Another positive aspect is the CO2, energy and H2O saved in producing this packaging.
%
Solar energy
Tonnes of CO2 saved every year
%
Sustainable packaging
THE GREEN IMPLANT
We strive to drastically minimise the environmental impact of all our products across their entire life cycle, from raw material through to the end of their product life This means we can do our bit to keep our ecosystem intact and to leave a neutral footprint, as an environmentally sustainable company. We work according to mandatory standards and voluntary internal commitments.
Königsee Implantate GmbH Achieves Milestones in Eco-Friendly Medical Technology with “GreenImplant” Concept and Earns EMAS Certificatio
Königsee Implantate GmbH has successfully obtained certification under the Eco-Management and Audit Scheme (EMAS), highlighting its commitment to environmental protection and sustainability in the medical technology industry.
EMAS is a voluntary instrument of the European Union that assists companies and organizations in managing their environmental impacts, continuously improving, and transparently reporting on their environmental performance.standards.
Companies validating under EMAS commit to setting environmental goals, implementing environmental management systems, and conducting regular environmental audits. Participation in EMAS demonstrates their responsibility for environmental protection and sustainability in a verifiable manner.
EMAS goes beyond mere compliance with environmental regulations by encouraging companies to proactively set environmental goals and continuously minimize their environmental impacts. It is a significant tool for companies aiming to enhance their environmental performance to the highest
Founding member of the “Unternehmensnetzwerk Klimaschutz” (the company network for climate protection)
We have been a founding member of the “Unternehmensnetzwerk Klimaschutz” since April 2022. This organisation is funded by the German Federal Ministry for the Environment (“BMUV”) as part of the national climate protection initiative. The project is supported by DIHK Service GmbH of the Association of German Chambers of Industry and Commerce. The network was founded for companies invested in climate protection and an environmentally conscious approach. Would you like to become a member? Click here for more information
Success born of sustainability
Sterile packaging
There is a trend in the field of medical technology at the moment for sterile packed implants. While we, as a company, are fully focused on innovation and change, we are sceptical about this trend. The flip-side of sterile packaging is the enormous increase in the volume of packaging, the resulting astronomical extra costs for packaging, logistics and disposal, rising processing costs in hospital and, above all, the severe detrimental impact on the environment. Königsee Implantate has made at least some of its packaging recyclable, by more or less avoiding composite materials and using cardboard that has already been recycled. Storage volume: We ensure that our packaging sizes are space-saving, to save on packaging material, storage space and shipping volumes.
Outer protective packaging
In collaboration with puracon GmbH we have found suppliers who offer packaging made 100% of recycled paper. This means we completely avoid the use of virgin fibres. Another positive aspect is the CO2, energy and H2O saved in producing this packaging. By avoiding additional packaging such as the additional stretch film used as standard for sterile packaging, Königsee Implantate saves on a considerable amount of plastic in the form of LDPE, without affecting the safety or quality of the products.
Double sterile barrier
We have also been able to optimise the statutory double sterile barrier. The composite materials mentioned above are either difficult to recycle or cannot be recycled at all. This is why we avoid these materials in as far as possible in the “internal” sterile packaging. The packaging consists of sealed PA-PE foil. We are also currently switching the non-sterile packed products to this type of packaging.
Solar energy for our products
Training project design solar farm
The sustainable solar farm from Königsee Implantate is one-of-a-kind. This unique project brings everything together in a single hub: An annual saving of 200 tonnes of CO2, thriving flora and fauna around the site in Aschau and the involvement of trainees who have bolstered their skills and expertise by working on this project. The team had to prove their team skills in producing this piece together, constructing a solar farm model with “THEIR” material – metal. They also had to work with intense focus on structuring and organising the training operation, environmental protection and the planning and organisation of the work. And all this not just by following the training manual, but hands-on and as a team project.
Generally, trainees at Königsee Implantate tend to be separated from the rest of the company for the first two years and concentrate solely on their practical skills. Only in the third year, by which point they are have honed their skills, are they integrated into the ongoing business. Training in the company has always been very well-structured, so nobody needs to be worried that they will end up making teas and coffee all day. The “Solar farm project” is a step further still. A new and holistic blend of sustainability mixed in with the content of the metal worker training to become a machining engineer. Purely vocational content is interfaced with rethinking what we know to secure our future quality of life – and that means working life too. Königsee Implantate proves that you do not need to be a corporate group to implement holistic measures of this kind and hopes that other companies will be inspired to follow our lead.
Solar farm and biotope
At Königsee Implantate, we are working hard to keep our ecological footprint as small as possible. Once we had ensured that all sites had photovoltaic systems, in 2021 it was time for a larger solar farm. This reduces the company’s CO2 emissions even further and means that we produce more of our own electricity. The construction of a solar farm on what was once a meadow would have had an impact on natural habitats. So our aim was to give space and life back to nature with a sustainable design.
Shelter for a diverse range of insects and animals
The height of the solar panels means that grasses and other plants can grow underneath them, with space for man-made insect hotels and other spaces for shelter for a very wide range of domestic insects, amphibians and reptiles. Natural materials were used to create the shelters. Harmful plants such as ragwort, which is poisonous to humans and animals, were removed from the land.
Conserving resources
Rebuild not new-build
Walking instead of driving means more time for your family. These are the cornerstones by which the Königsee site lives. When choosing our location, Königsee was not some random choice. The advantages are self-evident: Many of the employees in the logistics centre live in Königsee and can walk to work. You can get to the local nursery school quickly in emergencies.
Existing building substance used
When converting the logistics centre it was important to us to incorporate a wealth of resource-saving details. Even the energy needed to run the building is from our very own photovoltaic system. Several existing buildings have been converted to company sites, rather than building new ones (building recycling):
- Kid’s holiday park turned into training centre
- Butcher’s shop turned into coatings centre
- Shopping centre turned into sales and logistics centre
Autonomous training centre
We have also invested in sustainability at our training centre: A new photovoltaic system with a total output of 20.15 kilowatt peak (kWp) supplies the building with solar power. The new PREFA roof holds 62 modules that together generate about 21,000 kWh a year. A TESLA battery system with a capacity of 13.5 kWh saves any energy not needed during the day; this is then used in the training centre for energy consumed at night. With an annual saving around 12 tonnes of CO2 emissions, Königsee Implantate makes a valuable contribution in its responsibility towards the environment and future generations.
Award winner in 2017
We won the Thuringia Energy Efficiency Award in 2017 for our heat management. This energy efficiency award from the German state of Thuringia has been running since 2012, and is awarded to communities and companies in the free state that go the extra mile for climate protection and energy efficiency and for saving energy and resources. It recognises excellent projects and concepts that show what can be done in Thuringia with technical know-how, ideas and courage. This showcases the wide-ranging commitment and success of companies and municipalities in Thuringia and motivates others into action.
Sustainable heat management
Other environmental projects:
- Static automatic energy data recording to prevent unnecessary standby consumption
- Use of virtual servers in the company to record data
- Conversion to cool the server room, separating it into cold and warm spaces
- Use of speed-controlled refrigerating machine and fans as well as additional heat exchangers to recover waste heat
- Automatic central ventilation of the production halls with heat recovery by connecting to the ventilation system of the former grinding department
- Additional bypass for energy-saving exhaust air feedback outside working times
- Highly efficient counterflow plate heat exchangers